Engineers Apply Skills to Out-of-the-Box Projects
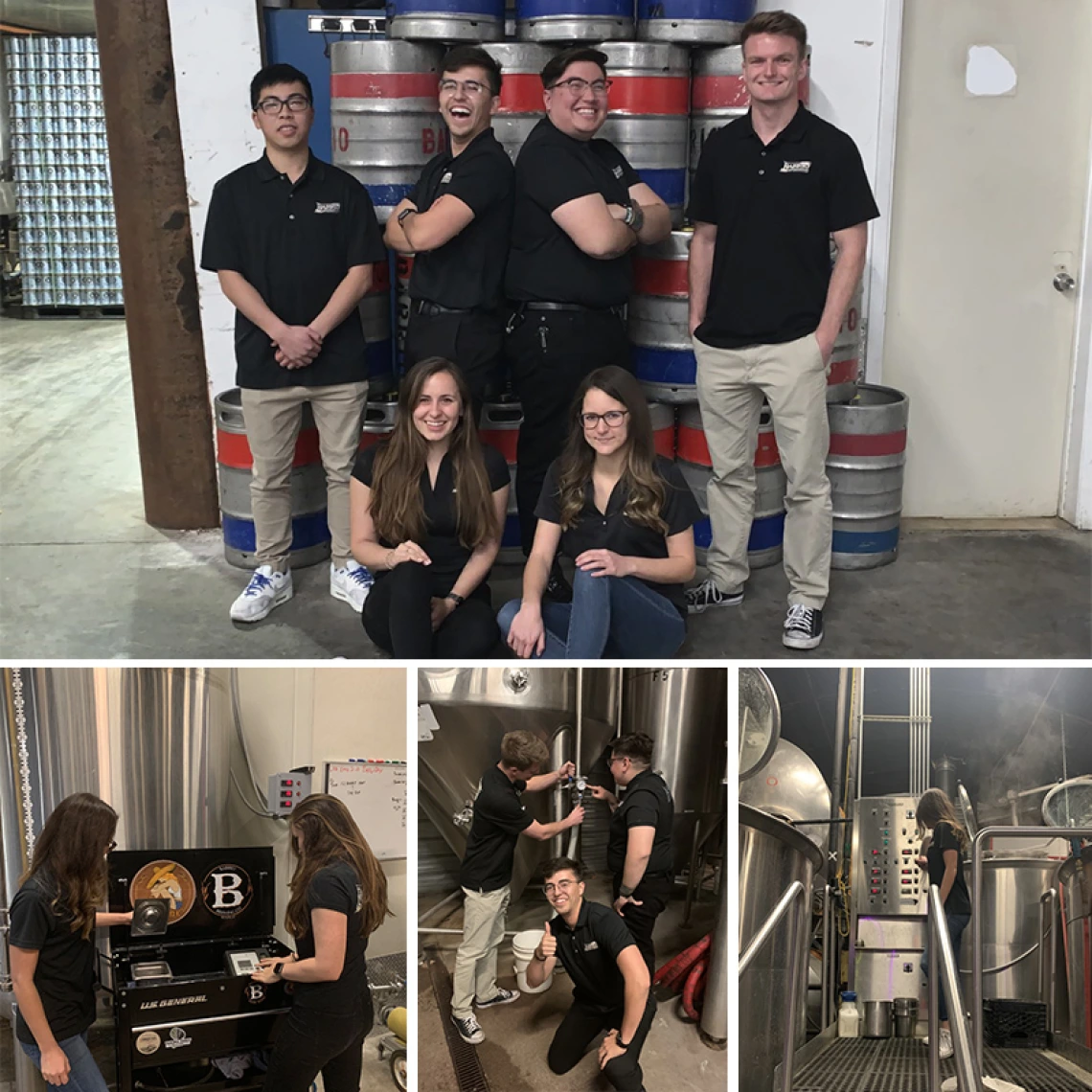
Team 19055 learns the details of brewing at Barrio.
The technical skillsets engineering students build at the University of Arizona – such as writing code and designing and building machines – often go to good use at engineering-focused companies. However, these skills are also necessary to keep a wide range of businesses running, such as restaurants, ceramics factories and breweries. Three capstone projects, sponsored by such companies, exemplify how engineering is something that impacts all facets of life.
Rolling Taquitos
Mateo Otero, chef and owner at Rollies Mexican Patio, used to work for Greek life at the University of Arizona. When he opened his own restaurant specializing in rolled tacos, or taquitos, in 2017, he quickly found he was selling about 800 each day. While looking for a way to make the rolling process more efficient, he recalled his days on campus, where he often saw engineering students working on their senior projects.
“I thought that bringing a fun project like a taco rolling machine to the senior students at the University of Arizona would be different and fun,” he said. “I’ve seen firsthand what the students are able to create and complete so I never had a doubt that they could do it!”
The students of Team 19042 are developing an automated machine that should be able to coat a tortilla in oil, fill it with stuffing, roll the tortilla, and apply a flour paste – 300 times an hour.
“This project is going to be a game changer for my business,” Otero said. “I’ll be able to cut back on costs and grow at the same time.”
Smoothing Edges
David Sounart is the VP of manufacturing at HF Coors, a Tucson-based ceramics manufacturer and seller. Dave Gilblom, a mentor for the capstone program, is a frequent customer of HF Coors, and the two men have had many talks about ceramics automation. While many parts of the HF Coors factory are automated, Sounart is turning to Team 19051 to extend the capabilities of a particular mechanism.
The existing machine smooths out the edges of round pieces using a stationary spinning sponge, which applies just enough pressure to remove excess clay from the piece as it rotates. However, the factory also produces plenty of pieces that aren’t round.
“We wanted something where we could put non-round shapes, like ovals and rectangles, and have the sponge move to track the edge,” Sounart said. “Right now, we have to do them by hand.”
Sounart is pleased with his team so far. They’ve successfully incorporated his feedback into their work, and they’ve visited the factory several times to get a feel for how the machinery works.
Chilling Out
Dennis Arnold, brewmaster, owner and founder of Barrio Brewing, has long been acquainted with UArizona engineers. Many have worked in his Tucson brewery over the years, and his daughter is a senior in systems engineering.
Arnold designed the chilling system at Barrio himself, making many adjustments along the way. A large part of the process for Team 19055 is to come in and survey the system’s current state. That means measuring every piece of pipe and examining every motor pump and compressor.
“We’ve been such a mom and pop shop, building our own things and seeing what flies,” he said. “With 28 years of adding to a system, you’re never going to have blueprints.”
After the team concludes their initial analysis, they’re tasked with determining the optimal way for the system to run. They will then identify the deficiencies between the ideal set up and the current state. Finally, the team will design a prototype for a more efficient, affordable method.
“This will take us into the 21st century, in a way,” Arnold said.