Engineering Seniors and Alumnus Team Up to 3D-Print Face Shields
When the campus closure foiled this team’s senior project plans, students turned their focus to creating face shields to protect health care workers from COVID-19.
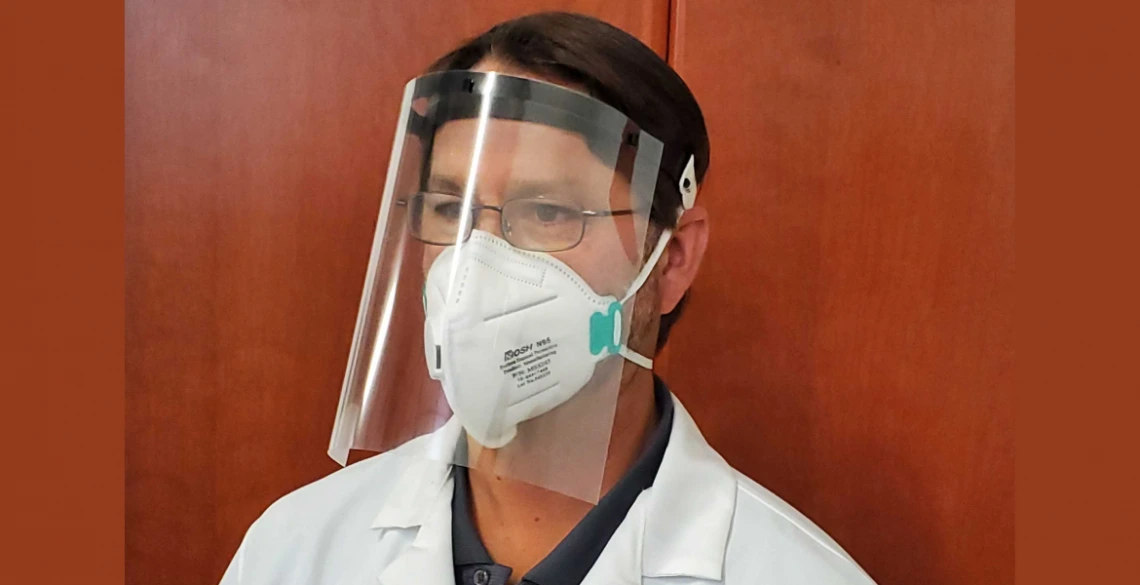
This year’s students have learned better than most how to adapt to life’s curve balls. Less than two months before Craig M. Berge Design Day, the university shut down facilities in response to COVID-19, and seniors found themselves scrambling to complete yearlong projects.
One Interdisciplinary Capstone team didn’t have access to equipment necessary for wrapping up development of an automated 3D-printing process. But sponsor company Micro FDM enlisted the students help on a new project that built on much of the work they’d already done.
“Hey, since you’re not able to finish the project, how about we change gears and build a printer, at lightning speed, that can print face shields?” asked Erik Orwoll, co-founder of Micro FDM and industry mentor for the project.
A face shield is a thin sheet of clear plastic, attached to a headband, that acts as an extra layer of protection for health care workers by covering the wearer’s face and neck.
Miranda Albo and Scott Bankofier, mechanical engineering; Shawn Dhani, systems engineering; Harsha Dhanraj, industrial engineering; Alex Doumas, biosystems engineering, and Abdi Tasir, electrical and computer engineering ll jumped at the chance to help.
“Our team recognized the magnitude of this issue and decided that any footprint we could leave on the road to decreasing the number of COVID-19 cases, we were willing to do it,” said team leader Bankofier.
Crisis Response Design
The six students had spent most of the year developing a way to automate the 3D-printing process for Micro FDM. When a 3D printer finishes printing an object, a person typically needs to move the object aside so another item can be printed, meaning it’s not possible to do round-the-clock 3D-printing without oversight from personnel.
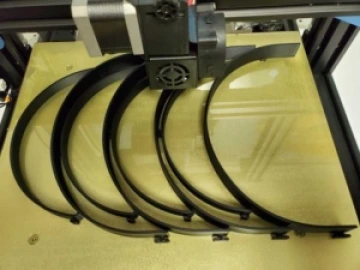
Automating the 3D-printing process means a machine can print one item after another without personnel needing to move the objects aside. Here, four shields are nested together after being consecutively printed.
Tasir, the team’s only electrical and computer engineering student, is developing a feed system driver, or FSD, that integrates with Micro FDM’s existing 3D printer to automate this process.
“The FSD will communicate with the 3D printer’s firmware to load and unload cartridges, or print platforms, so that it can print multiple face shields in one print session,” he said. “This will limit the human interaction with the printer and make the process a lot faster.”
The team also helped design a shield that’s easier to 3D-print, enabling the setup to 3D-print four shields at a time. The first time Micro FDM printed a face shield, it took about an hour and 40 minutes, but within two weeks, the company decreased the printing time to 27 minutes. Now Micro FDM is producing 20 face shields a day and aims to increase production to 50 per day. The goal is to ultimately ship out 5,000 shields every 10 days to health care facilities.
Hands-on Health Care Experience
Interdisciplinary Capstone is a part of the college’s Craig M. Berge Engineering Design Program, which provides undergraduate students at all levels with hands-on design experience. Orwoll turned to the team because he wanted them to get just that, and to have a physical, finished product to show prospective employers. Plus, the company needed extra hands for the project.
“It’s exciting because we’ve got this team of engineers whose expertise we can draw on,” said Orwoll, who earned his bachelor’s degree in mechanical engineering from the UA in 1989. “This is similar to the project they were already working on, so we thought, ‘Let’s take advantage of that with an effort that can help society.’”
The students have become invaluable to Micro FDM’s shield-making taskforce. Some team members are investigating health care specifications for face masks, and others are working on designing a box for shipping the unassembled face shields to hospitals. They’ve spent the last few weeks in Zoom meetings and sending photos of prototypes back and forth.