Preparation pays off for teams with early prototypes
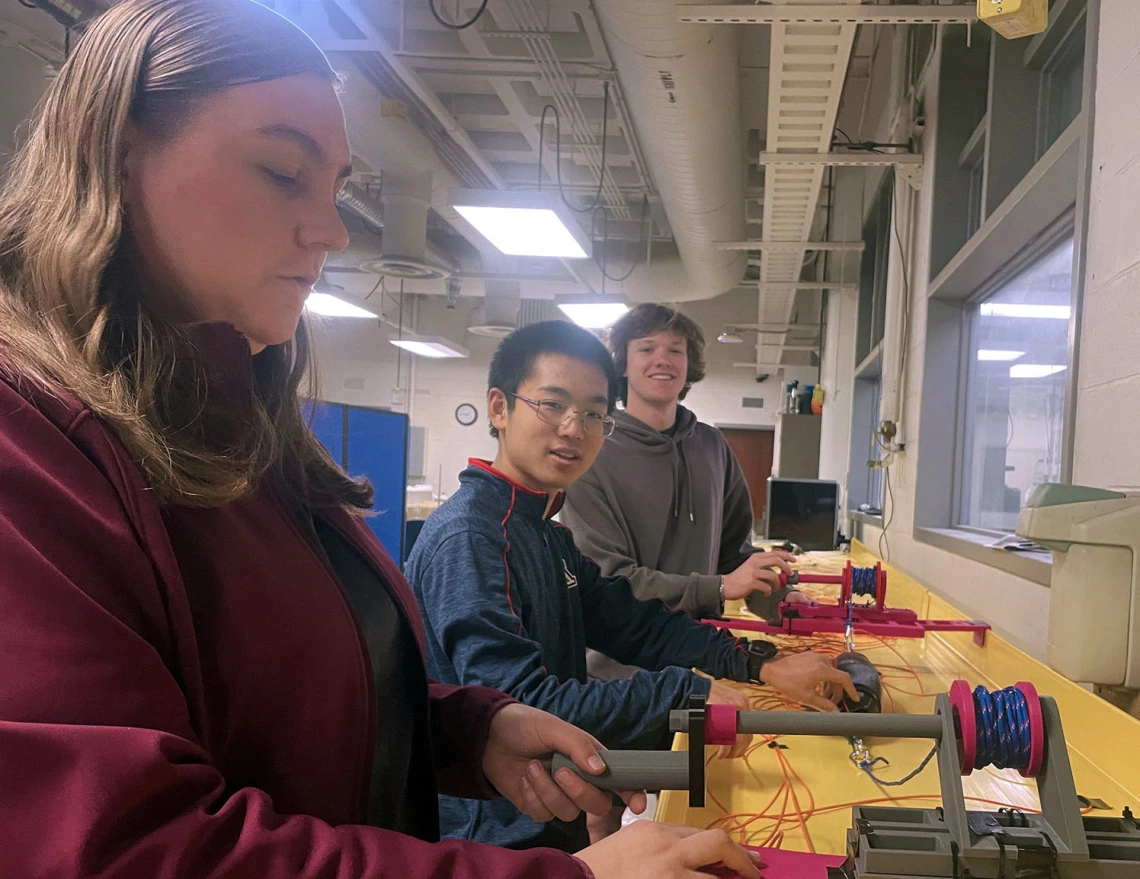
Team 25015 members (from left) Samantha Fisher, Joseph Lee and Will Zupancic adjust the cable tray mounts they designed and produced for making cables easier to manipulate in data centers.
With Craig M. Berge Design Day only a few months away, students are working hard to complete deliverables for their Interdisciplinary Capstone projects. Two teams that produced prototypes before the spring semester are well positioned to impress sponsors, judges, peers and family members on May 5.
A first for seaplane design
Nyhel Sekulic is the student leader for Team 25011, which is helping sponsor The New Nose Company develop a long-range amphibious seaplane that can deploy divers and submersibles at sea, as well as support maritime surveillance and search and rescue capabilities.
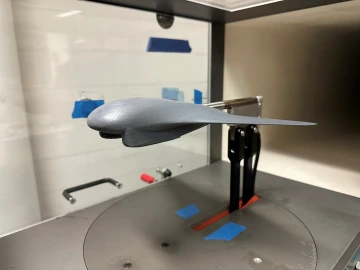
Team 25011 produces its blended wing seaplane prototype using a 3D printer in the Engineering Design Center.
The design is the first seaplane of its kind, said Sekulic, as it uses a streamlined shape known as a blended wing body.
“The wings merge with the body to improve aerodynamics,” she said.
Because blended wing bodies are typically used for military jets, the students are exploring novel territory by integrating the shape into an amphibious craft.
The students met their goal to produce the representational prototype by mid-November. This meant they could perform preliminary wind tunnel testing in time for their critical design review in early December. At CDR, engineering experts provide feedback on each team’s plans and progress.
The team has kept on track with the help of “some pretty rough deadlines” they set for themselves, said its leader. Following CDR, Team 25011 is performing additional wind tunnel testing, looking to maximize the plane’s lift and minimize drag. The students are also analyzing performance using computational fluid dynamics, which simulates the air and water conditions the craft will encounter.
With further results gleaned from testing and CFD analysis, the team plans to continue making improvements and arrive at a design with the best possible lift-to-drag ratio.
“We have a mix of good communication, good time management, and also a big love for what we're doing,” said Sekulic, a systems engineering major who hopes to work with CFD in the motor sports industry.
Custom cable system reduces work risk
Another team that was well-prepared for CDR will also keep polishing its deliverables until Design Day. Seven students, led by mechanical engineering major Joseph Lee, are working with Microsoft to better manage active optical cables (AOCs) in data centers.
As artificial intelligence and other high-performance computing needs grow, more AOCs are needed to connect devices such as routers and servers. Microsoft positions the cables in trays 10 feet above the ground. The students’ winch and pulley system allows workers to space the ladders farther apart and spend less time on them, making the process both quicker and safer.
The system is customized to work with Microsoft’s cable trays, which have varying widths, and cables of differing diameters. The students designed most parts from scratch.
“It’s been a good experience to work on that and to work with the team making designs and drawings and doing the analysis to back it up,” said Lee, who will continue in the University of Arizona accelerated master’s program for mechanical engineering after graduating.
In addition to effective scheduling and teamwork, Lee said the review process – which also includes a preliminary design review – has helped his team iterate with confidence. At Design Day, they plan to present a product the sponsor could use as a long-term solution.
“It’s been helpful to hear feedback twice from people who have spent a lot of years in industry and have done a lot of design reviews. They’ve seen projects that have succeeded and not succeeded,” he said.