Students integrate sustainability in unexpected ways
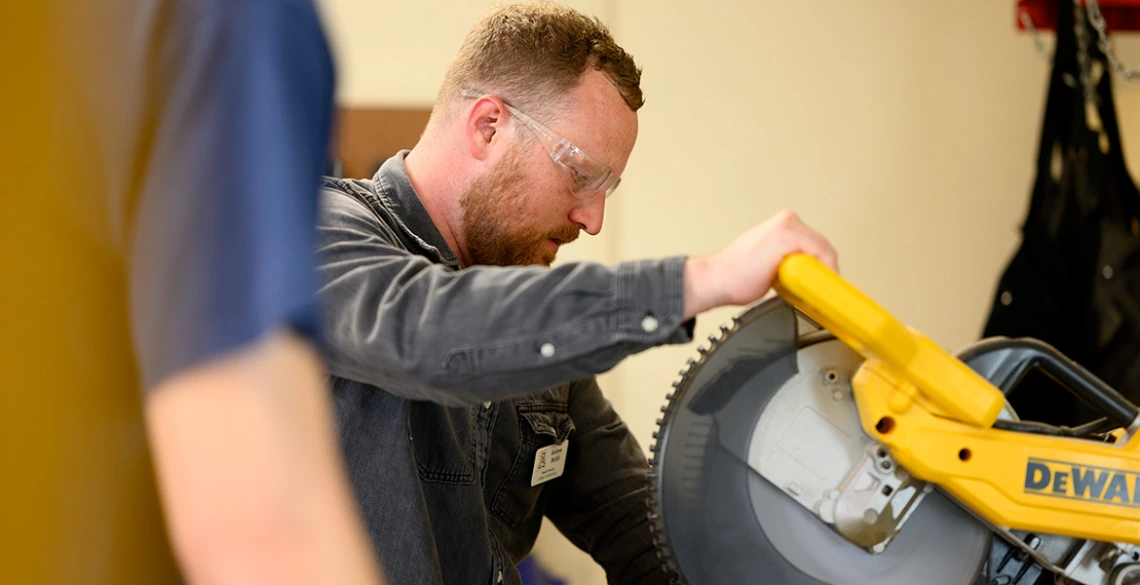
Teams like 25025 use tools in the Engineering Design Center to create replicable parts for their Interdisciplinary Capstone projects.
The Interdisciplinary Capstone faculty introduced updated program requirements at the 2024-2025 Craig M. Berge Design Day Open House.
“It’s important that we teach our engineers to always be thinking about sustainability as they design,” Steve Larimore, lead program instructor, told the sponsors.
Teams are now required to approach their designs with an environmentally conscious mindset and have freedom to decide where that requirement is met.
Two teams have approached their projects with very different strategies.
Stabilizing temperature with scrap metal
Capstone Team 25047 is developing a multichambered box for sponsor Raytheon, an RTX business, that will control temperature and humidity for storage of 3D printer filament.
Filaments are materials fed into 3D printers that turn digital designs into a physical product. Raytheon’s Additive Manufacturing Lab in Tucson uses filament to print a variety of items for customers, but proper storage has been a problem. Filament must be stored in low humidity and requires preheating before it’s fed into the printer.
“Right now, they’re storing filament in Tupperware-like containers to try and preserve it from the humidity, and they don't have any way to preheat them,” said Ryan Raad, project lead and electrical and computer engineering major.
Proper storage will reduce waste, but they also plan to approach sustainability in other areas, including power usage and material sourcing.
The storage box will need a lot of power to heat the filament.
“We plan to have the heater automatically power off when it reaches the desired temperature,” Raad explained. “And we're really focusing on achieving a low thermal bleed on our system.”
To save on power usage, the team will integrate high-quality insulation to keep heat inside the box.
But the team didn’t stop there. On Nov. 4, Raad and the crew visited Raytheon to scout scrap material and waste on the property that could be used toward the project.
“We're trying to use all recyclable materials,” Raad said, adding that doing so also reduces cost for the sponsor.
Sustainability through a new lens
Team 25025 is developing an automated microscope slide transfer module for Roche Tissue Diagnostics to automate a tedious part of the diagnostic process.
Histology technicians prepare human tissue samples for pathologists to identify possible diseases, so the organization and categorization of each sample slide is incredibly important. But this preparation process is also extremely repetitive.
Student team leader Kerwin Dewberry Jr said his team plans to fully automate this process with their module by cataloging up to 20 microscope slides at a time. The module will move the slides to take a picture, check for contamination, and read the slide’s barcode to match the collected information with the unique sample before sending it off for further analysis.
“This frees up more time for technicians and pathologists so they can focus on diagnosing patients rather than doing these menial tasks,” said Dewberry, an aerospace and mechanical engineering major.
And he speaks from experience. Between his first and second year, Dewberry interned with Roche and saw the whole process play out, noting that technicians had to perform that process by hand repeatedly.
The team will split the project into three main parts: slide movement, slide pick up and camera assembly.
“Every single one of our components has a sustainability factor,” Dewberry said.
The slide movement component, called a gantry, will be made with aluminum rods, which are easily recycled.
“We can also shave them down if we need something new,” he added. They can reshape the rods for other components or design adjustments.
For the slide pick up component, the students plan to 3D print parts in the college’s Engineering Design Center. These parts can be replicated and individually detached or clipped in, meaning the design won’t require buying an entirely new system if one part breaks.
The team approached the camera system with the same inspiration by using a lens that easily screws in and out so the sponsor can switch out lenses without buying new camera housing.
Dewberry said the sustainability requirement has been relatively easy to integrate, due to the work of talented teammates.
“This [project] gives us the ability to go and do something not constrained by an assignment,” Dewberry said. “It gives us the opportunity to be engineers and be creative.”