Coming Soon: Wind Turbines in the Ductwork
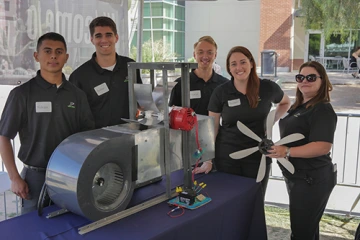
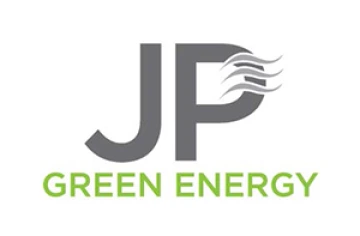
Project Title: Method and System for Air Velocity Generated Electrical Power
Team 16028 Members:
Thomas Joseph Deranek, industrial engineering
Austin Karl Hoepfner, mechanical engineering
Hannah Elizabeth Ingle, electrical and computer engineering
Heidi Lynn McCook, electrical and computer engineering
Fabian Javier Medina, mechanical engineering
Sponsor: JP Green Energy
JP Green Energy-Supported Team Tests HVAC Airstream Power Generation
JP Green Energy, a Tech Parks Arizona tenant, is developing technology to help bring the power of wind turbines, widespread throughout rural America, closer to home. The startup is developing a way to generate electrical power from airflow in residential and office heating and cooling ducts.
With the help of 2016-2017 Team 16028’s prototyping and testing, company founder Pierre Abou-Zeid was looking to improve the design of his small-scale energy generating system and move it closer to commercialization. The park’s collaborative atmosphere led him to the Engineering Design Program.
“It was more financially feasible to be a sponsor than hire employees,” said Abou-Zeid, whose company is a client of the park’s business incubator, the Arizona Center for Innovation.
The project marked the first partnership between the program and a startup at Tech Parks Arizona, which connects companies with University resources. But it won’t be the last. Given JP Green Energy’s positive experience, more of the park’s 40-plus companies will be working with student teams from the Engineering Design Program, said Bruce Wright, UA associate vice president for Tech Parks Arizona, part of Tech Launch Arizona.
Senior Design Team an Affordable Option
The students were tasked with prototyping and testing designs for easily manufactured HVAC wind turbines. Their goal was to determine the best options for minimum air resistance and maximum power generation from a typical heating, ventilation and air conditioning duct airstream of 750 to 1,000 feet per minute. They accomplished maximum power generation by modifying their blade design for higher torque and incorporating a more efficient generator.
As with any wind turbine technology, blade design is critical to the system. The team tested three turbine blade designs. One was Abou-Zeid’s creation, for which he received a U.S. patent in 2013. The other two, including one created with a 3-D printer at the Arizona Center for Innovation, were developed by the students. They considered blade size, pitch, shape, and insertion depth while focusing on motion, stress and structural integrity.
The student designs were less turbulent but had lower power output than Abou-Zeid’s original blade, which generated 5.73 watts of power output without a turbulence-minimizing cover and 3.81 watts with the cover. The small output numbers represent what can be harvested from the kinetic energy in airflows generated by household heating and cooling equipment. Larger-scale equipment would generate higher outputs.
“As long as you have a minimum airflow of 1,000 feet per minute, this design will work,” said Abou-Zeid. “The team improved on our initial test results. We will use the information to further improve our design and move toward commercialization.”