Precise Putter Performance Testing
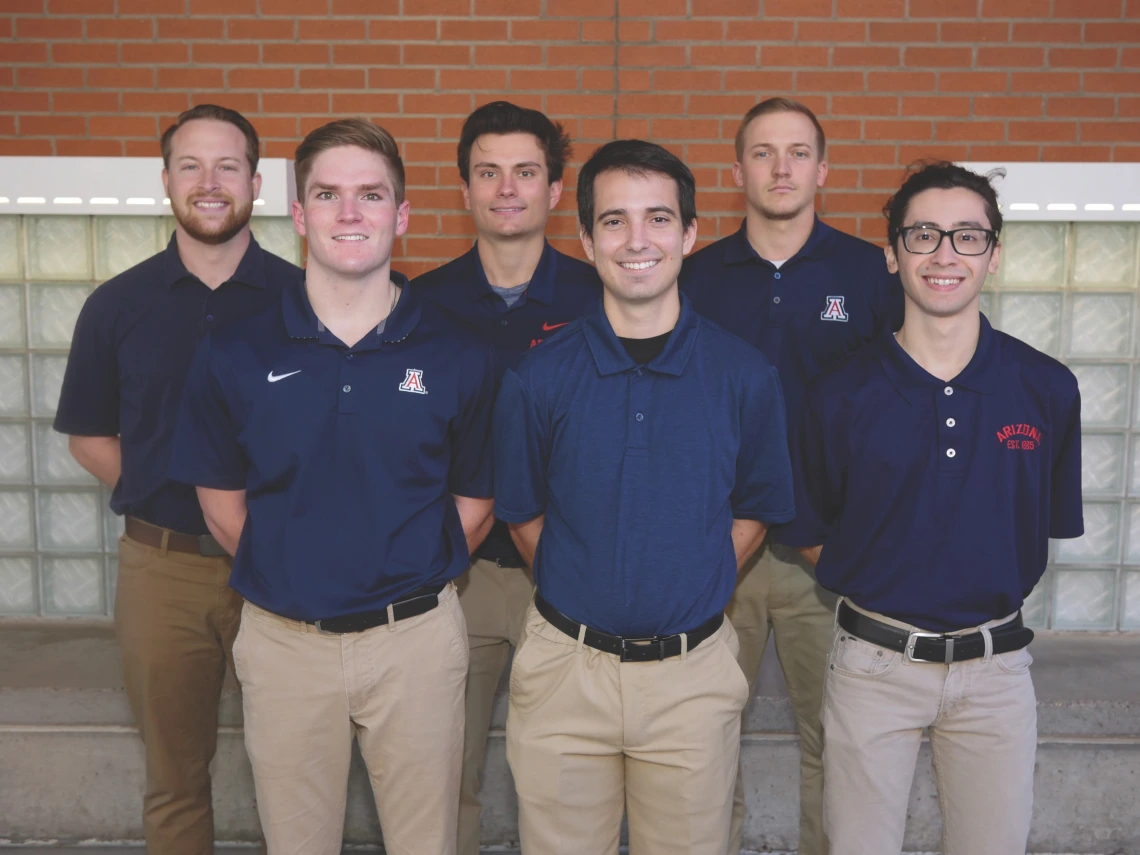
Project Title: Mechanical Putter Performance Pendulum
Team 22008 Members:
Austin M. Davis, mechanical engineering
Eric Marcos Lawson, electrical and computer engineering
Steven Perry, mechanical engineering
Jesus Alberto Serrano, project lead, industrial engineering
Ian Kyler Shaw, mechanical engineering
Nathan Eric Wolff, electrical and computer engineering
Sponsor: PING Inc.
At sporting equipment manufacturer PING, engineers design and develop new putters and test their performance in different situations. The Phoenix-based company sponsored its second Interdisciplinary Capstone project and tasked a student team with building a robotic pendulum which can grip and swing a PING putter the same way a golfer would.
But, unlike a human golfer, the machine can hit a ball with a putter from precisely programmed angles and at specific speeds. And it has no bad days.
The data generated by the machine will provide crucial insight into the performance capabilities of new prototype putter technologies to optimize the products’ design prior to launch, said project contact and PING Analysis and Testing Manager Tom Trueblood.
“It gives us that good balance of understanding what's possible and then, when we get it into a player's hands and measure what they actually do, we can compare and contrast and connect those dots between the theoretical and the practical,” Trueblood said.
Getting to the Awesome Part
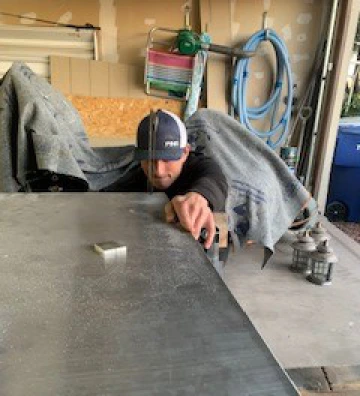
Mechanical engineering student Ian Shaw cuts a shelf for the mechanical putter performance pendulum’s frame.
Team procurement lead Steven Perry, a mechanical engineering student and avid golfer, was eager to contribute to a project likely to improve a product he uses.
“Once this is testing new putter head technologies, perhaps maybe a pro or even I would buy the new developed putter, and I can say, ‘Yeah, I built the thing that tested this,’” said Perry. “It’s an awesome feeling.”
Focusing on procuring parts and materials was a valuable learning experience for Perry, who maintained a detailed parts inventory as part of an internship at Raytheon last summer. And procurement ended up being the entire team’s most difficult challenge, said mentor Huy Le. Supply chain issues delayed delivery of some of the pendulum’s critical parts until March. Le worked with the team to find solutions.
“They immediately problem-solved and got around it so they wouldn’t fall behind,” he said.
The team planned ahead as much as possible and tested with similar parts in some cases so they could drop in final parts with confidence when they arrived.
‘Looking at the Future’
Perry looks forward to demonstrating the mechanical putter performance pendulum at Craig M. Berge Design Day.
“I’m excited for the oohs and aahs of the students who come out and say, ‘Wow, that's cool – you can make it putt from 10 feet, 15 feet, 30 feet.’ And I’m excited to showcase that we're not just going to school, we can actually do something with the skills that we gained, make a system that will do what we wanted it to do,” he said.
Le agrees. He’s an electrical and computer engineering alum from the class of 2015 and has been an Interdisciplinary Capstone sponsor as well as a mentor. No matter how many Design Days he attends, he said, there’s still a magical feeling to them.
“There's a buzz in the air. The whole university gets excited because the students are out on the Mall doing really cool things,” he said. “You're looking at the future here – our future leaders and industry partners – and seeing all their hard work pay off in this moment.”
After this competition concludes, Trueblood anticipates PING will sponsor additional Interdisciplinary Capstone projects. Last year’s project to automate the loading and unloading of golf shafts was also a success, and even won the Ergo Dave Award for Best Use of Human Factors Engineering at Design Day 2021. It also led to the company hiring student team member Truman Louth.
“Pulling in different, fresh perspectives from students has been really valuable for us,” Trueblood said.